Le béton au ciment Portland a envahi les chantiers de construction, que ce soit pour des maisons individuelles, des Etablissements Recevant du Public (ERP) ou des bâtiments collectifs, d’habitation ou tertiaires. Est-ce, était-ce inéluctable ? Est-ce, cela doit-il, être immuable ?
Beaucoup de questions qui ont déjà été abordées, développées ici et sur lesquelles nous reviendrons rapidement et succinctement.
Ce qui est relativement nouveau, c’est le mélange de ciment Portland et d’agrégats biosourcés.
Nous allons y consacrer cet article.
… Mythe ou réalité, … bonne ou mauvaise orientation, tout doit être abordé, démystifié ou validé.
Aboutirons-nous à une conclusion de greenwashing ou à une (des) piste(s) à promouvoir ?
Histoire du bâti français et du ciment
Avant le ciment
Nous avons déjà abordé les méthodes de construction antérieures à l’invention du ciment dans un article intitulé “La maison en construction, son histoire au travers des matériaux”.
Attendu que le ciment, tel que nous le connaissons actuellement, est relativement récent, 1840, la totalité de ce qui est antérieur à cette année là, et qui a été édifié par liaison d’éléments au mortier, l’a été sans ciment artificiel, commercialement appelé ciment Portland.
Attendu qu’il lui a fallu faire ses preuves et conquérir ses parts de marché, l’immense majorité de ce qui est antérieur au XXème siècle a été édifié sans ciment artificiel…
Nous avons donc su, pendant fort longtemps, nous passer de ses services.
Depuis l’invention du ciment Portland
Cet aspect historique a été largement développé ici dans un article intitulé “Comment les cimentiers nous trompent avec de vrais infos”.
Un petit rappel de son histoire :
Le ciment est un liant, d’autres existent dont la terre, le plâtre et la chaux. Leur emploi est bien antérieur à celui du ciment tel que nous le connaissons maintenant.
Il a été inventé par un français, Louis VICAT.
Auparavant James Parker, en Angleterre, avait découvert les caractéristiques d’une chaux très fortement hydraulique et qu’il baptisa “béton romain”.
C’est le Baron Vicat qui en établit le principe actif en 1818. Comme pour une chaux classique, la température de cuisson est de l’ordre de 900°.
Voulant laisser ses découvertes libres de droit afin qu’elles profitent à un maximum de gens, il ne déposa pas de brevet.
En 1824, un anglais, Joseph Aspdin, déposa un brevet pour une chaux à prise rapide, en fait le 1er ciment artificiel, qu’il baptisa commercialement “ciment Portland”. Celui qui posa les principes de prise, de formulation et de fabrication est Louis VICAT, en 1840.
La première usine vit le jour à Boulogne sur mer en 1846
A l’échelle du temps de la construction de maisons individuelles, c’est une invention récente.
Place du ciment artificiel dans la construction
Nous avons déjà développé ici dans divers articles, particulièrement ceux sur l’histoire de la maison en France et les affirmations des cimentiers, les raisons de son hégémonie actuelle, il ne nous semble pas nécessaire d’y revenir.
Voyons sa part dans l’édification des murs de nos maisons depuis la fin de la seconde guerre mondiale.
Nous sommes un des pays qui, bien que disposant d’autres possibilités en terme de matériaux, construit le plus en béton au ciment Portland : dans les années 1960 70 et 80 on a navigué aux environs de 80% pour revenir, actuellement, à 65% des maisons individuelles.
Les autres principaux modes constructifs auxquels il est fait appel sont les briques de terre cuite ou le bois, même si, pour ce dernier, de nombreuses infos, souvent défavorables, sont véhiculées à son sujet.
Les avantages du ciment artificiel
- technique connue et maîtrisée,
- grande disponibilité de maçons sachant le mettre en œuvre,
- grande disposition du matériau,
- technique relativement rapide (notamment par rapport aux techniques anciennes de maçonnerie à la chaux),
- constructions parmi les moins coûteuses au m2,
Les inconvénients du ciment artificiel
- matériau fortement consommateur d’énergie lors de sa fabrication,
- murs peu perspirants (ne laisse pas facilement migrer la vapeur d’eau),
- consommation de ressources fossiles et donc limitées (sable entre autres),
- émission de Gaz à effet de Serre, particulièrement du CO2,
Avenir du ciment
Les inconvénients listés ci-dessus, couplés à l’augmentation prévisible du prix de l’énergie (pour rappel, nécessaire en grande quantité pour sa fabrication), ont un impact négatif sur ce produit.
Les législations évoluent, notamment en France avec l’arrivée du label E+C-, base probable de la future réglementation thermique, prenant en compte l’impact carbone commencent à poser des problèmes aux cimentiers. Leur part de marché ne croit plus, bien au contraire.
Les meilleures années, 2006 et 2007, l’industrie cimentière a produit, de par le monde : 22,268 millions de tonnes de ciment (pdf). Depuis, leur part de marché ne cesse de baisser avec, dernier chiffre connu, 2016 : 15,934 millions de tonnes (pdf).
Cette tendance semble inéluctable et les cimentiers, de façon totalement légitime, cherchent à l’endiguer.
Réponses des cimentiers
Plus vert que vert
Ils essayent de nous convaincre que leur produit est tout à fait adapté à nos besoins, presque plus vert que vert. Ceci a été largement abordé dans ces colonnes dans l’article déjà cité ci-dessus : “Comment les cimentiers nous trompent avec de vrais infos”.
Ils l’intègrent dans des solutions présentées comme plus rapides, plus sûres, plus, plus, plus …
Intégration de leur production dans des matériaux à forte connotation sympathique
Depuis quelques années, de nouveaux bétons apparaissent intégrant, en tant qu’agrégats, des matériaux biosourcés.
Quelques exemples de produits ciment + biosourcé
Thermibloc, coffrage isolant
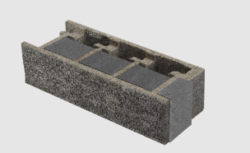
Nous sommes ici en présence d’un bloc qui, à la fois, sert de coffrage intégrant l’isolant et recevra un voile de béton.
Les parois sont constituées de bois issu de sciage direct, résidus de scierie. Ils sont constitués de 80% de bois et 20% de liant minéral.
Le béton de bois qui constitue le bloc a un lambda relativement médiocre puisque 0,10, ce qui est très insuffisant pour obtenir des résultats suffisants sans adjonction d’un isolant.
Celui-ci peut être soit du polystyrène graphité, soit du polyuréthane, soit de la laine de bois.
Après mise en place des éléments en continuité, après adjonction de ferraillage entre les rangs, un voile béton va être coulé en place. Il assurera la liaison des éléments, les reprises de charge des divers éléments, entre autres les dalles, et apportera l’inertie gage de confort.
Performances
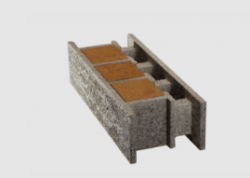
Le fabricant, Xelis, annonce une performance de R = 4,35 avec 16 cm de laine de bois pour un bloc d’épaisseur totale de 38 cm hors parements de finition, tant extérieur qu’intérieur. Dans un bloc identique mais intégrant non plus de la laine de bois mais du polyuréthane, on atteint un R de 6,97.
Compte tenu de l’épaisseur totale de la paroi, la 1ère performance n’est pas exceptionnelle, loin s’en faut. La 2ème est très bonne, mais quid de l’écologie avec la mousse PU.
Ecologiquement ?
Certes le bois utilisé est un piège à carbone, mais quel apport cela représente-t-il par rapport au carbone émis pour la fabrication du ciment utilisé pour le bloc lui-même et aussi (surtout) pour le béton du voile coulé en place (dans le cas du bloc 38/16, d’épaisseur totale de 38 cm, cité en exemple pour les performances de la laine de bois, voile de 15 cm d’épais).
Nous n’avons pas les chiffres, mais à n’en pas douter, le CO2 piégé est certainement infiniment moins important que le CO2 émis. N’oublions pas que l’industrie du ciment est un des plus importants contributeurs mondiaux pour les émissions de gaz à effet de serre.
Naturbloc bois
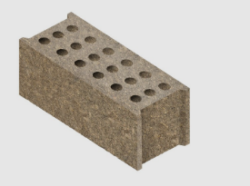
Nous sommes ici en présence d’un bloc béton composé de bois d’origine, entre autres, de palettes en fin de vie et de ciment Portland. Sa fabrication est conforme aux normes NF EN 14474 applicables aux bétons dont le granulat principal est composé de bois.
Le fabricant, ALKERN, nous annonce 28 kgs de bois au m2, ceci pour un poids total de 180 kgs (10 blocs au m2). Nous en concluons que le bois représente environ 15% du poids total.
Comme pour le bloc Thermibloc cité ci-dessus, il ne nous semble pas qu’il y ait un rapport important et intéressant entre le CO2 capté et fixé par le bois par rapport au C02 émis lors de la fabrication du ciment qui entre dans la composition des blocs en question.
Ce produit nous est annoncé 100% recyclable. Nous aimerions comprendre comment des composants, pour l’un végétal (l’agrégat), pour l’autre minéral (le liant) pourront être séparés aux fins d’être chacun recyclés …
Biomis G3
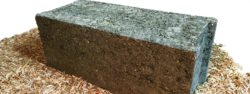
A nouveau un bloc qui pourrait se substituer au traditionnel bloc béton. Ce produit a été développé en lien entre 2 industriels, le groupe Calcia, fabricant de ciment et ALKERN à nouveau, fabricant de produits préfabriqués liés au ciment Portland.
L’agrégat minéral classique a été, ici, remplacé par un broyat de miscanthus.
Ce bloc ne semble pas encore complètement industrialisé, cependant ses promoteurs commencent à communiquer à son sujet.
Ils y intègrent une troisième entité : les producteurs de cette plante (pdf).
Nous comprenons que des agriculteurs puissent être intéressés par la recherche de nouveaux débouchés. Nous comprenons moins bien que des terres agricoles soient utilisées à la production de plantes destinées à l’industrie plutôt qu’orientées vers des productions directement à destination de l’alimentation pour les habitants de la planète, qu’ils soient animaux ou humains.
Ce nouveau bloc est donné pour une valeur R de 0,7 m2.K.W pour 20 cm d’épaisseur. C’est certes mieux que les 0,23 des blocs conventionnels à 3 parois ou même que les 0,51 des blocs à parois décalées en béton conventionnel.
Cependant, quel va être l’impact en terme d‘épaisseur d’isolant nécessaire pour atteindre un R total de 4, désormais classique en RT2012 ?
Quel gain espérer en terme d’économie d’épaisseur avec l’utilisation de ces blocs “Biomis G3” en lieu et place de parpaings conventionnels à parois décalées ?
Avec une classique laine de verre GR 32, il faudrait : (différence de R atteint) x lambda de la GR 32 = épaisseur exprimée en mètre, soit (0,7-0,51) x 0,032 = 0,19 x 0,032 = 0,0608, soit 6,08 mm de plus. Dit autrement : en utilisant des blocs béton conventionnels à parois séparées, il faudra plus d’isolant laine de verre GR 32 : + 6 mms …
Voilà le gain réel obtenu par ce bloc annoncé comme “totalement en phase avec la réglementation thermique” (extrait du site calcia) …
Conclusion
Ces 3 exemples sont assez représentatifs de la tendance actuelle. Ils nous sont présentés comme des solutions propres à économiser des agrégats issus de ressources non renouvelables (gravier, sable), ce qui est vrai. Mais n’existe-t-il pas d’autres solutions d’économiser ces précieuses ressources, entre autres en construisant avec des matériaux naturels simples et disponibles tels que le bois, la terre et bien d’autres encore, sans oublier la rénovation de bâtisses anciennes.
Une fois de plus, on nous présente des solutions soit-disant innovantes car meilleures que des solutions plus anciennes mais, être meilleur que quelque chose de moins bon ne fait pas, en soi, qu’une nouveauté est performante, elle peut être simplement moins mauvaise !
Nous pensons qu’il s’agit plus de soubresauts d’une industrie en perte de parts de marché, disons-le, sur le déclin (elle vient de voir sa production mondiale baisser de plus de 28% en 10 ans), que de véritables avancées techniques ou environnementales.
Pour nous, toutes les affirmations qui nous incitent à les utiliser car respectueuses de l’environnement, recyclables, permettant d’économiser des ressources fossiles, de limiter les émissions de CO2 relèvent de Greenwashing.
Nous comprenons l’impasse dans laquelle se trouvent les cimentiers et les essais divers de proposer des solutions et produits, plus ou moins pertinents, pour ne pas sombrer corps et âme.
C’est pour cette raison que nous risquons fort de devoir remettre cet ouvrage sur le métier encore de nombreuses fois, malheureusement pour eux, aussi souvent que nécessaire.